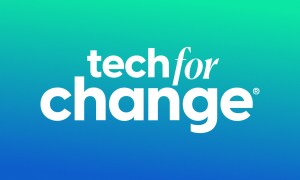
Is 3D printing the future of housebuilding? It certainly will be if new startup Mighty Buildings, which launched from stealth mode this week, has its way. The company builds houses rapidly using a giant 3D printer and proprietary 3D printing material that, unlike concrete, hardens almost immediately thanks to a UV light curing process. This technique allows it to create houses with 95% fewer labor hours and significantly less waste than traditional construction techniques, which could be a game-changer in the construction field.
“The 3D printing, robotic post-processing, and the ability to automate steps like the pouring of insulation means that Mighty Buildings will be able to automate up to 80% of the construction process,” Sam Ruben, chief sustainability officer and co-founder of the company, told Digital Trends.
According to Ruben, Mighty Buildings will be producing fully printed structures for customers within a year. Initially, these units will be created using a hybrid approach that is part 3D-printed and part traditional construction. However, once the “understandably conservative nature of building officials” is overcome through some neat demonstrations, Ruben said the startup will begin introducing fully printed units.
As a recent demo, it printed a 350-square-foot studio unit in less than 24 hours. It has also installed its first two “accessory dwelling units” in San Ramon, California, and San Diego, and additional units are currently awaiting delivery. Prices for the units start at $115,000 for a Mighty Studio and go up to $285,000 for a three-bedroom, two-bath Mighty House. That’s not exactly dirt cheap, but it’s certainly more affordable than a traditional brick-and-mortar building. Plus there’s all the bragging rights of telling your buddies you had your new home printed for you.
“Compared to typical prefab construction, one of the biggest differentiators of our system is the ability to quickly and easily customize designs without needing to lay out a whole new factory line,” Ruben said. “When so much of the structure can be 3D-printed, and when much of the post-processing can be done robotically, you unlock a lot of possibilities that would require very customized workflows if done with traditional prefab methods.”
This isn’t the first time Digital Trends has covered 3D-printed housing or other livable structures. But in most cases, these have been proofs of concept, rather than commercial offerings. Ruben said that the team plans to “open our production platform to a few forward-thinking builders, architects, and real estate developers in 2021. Looking beyond 2021, we also plan to build joint-venture partnerships to scale Mighty Factory prefab hubs anywhere in the world.”